Project-Driven Business
Runs on PlanAutomate
We help project-based organizations control costs, run leaner, and drive better project performance.
Run your projects from end-to-end in any industry.
Project Driven Business
Runs on PlanAutomate
We help project-based organizations control costs, run leaner, and drive better project performance.
Run your projects from end-to-end in any industry.
I’ve always liked the product that PlanAutomate puts together. It was the best decision that we made as a company.
Jeremy Grosser – President at Rex Moore
Tessitura Networks Optimizes Complex Projects with PlanAutomate
Tessitura Networks delivers specialized software solutions for arts and culture organizations around the world. They require robust Work Breakdown Structures (WBS) with intricate resource planning revenue-at-completion metrics, and WBS-based pricing—something standard tools couldn’t handle.
PlanAutomate provides the advanced project automation with scheduling, resource management, and revenue tracking they need—all seamlessly integrated within D365 Finance. With PlanAutomate, Tessitura can efficiently plan, allocate, and manage resources at scale, ensuring projects stay on track and financials remain aligned.
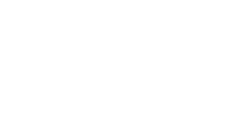
ICM Powers Project-Driven Production with PlanAutomate
ICM engineers, builds, and supports the biofuels industry’s most efficient and innovative ethanol plants. Success depends on precise project-driven production and procurement—ensuring the right materials are available at the right time.
With thousands of tasks and components in each project, aligning live project schedules with ongoing production is a complex challenge. Traditional tools fall short in managing this scale while integrating with MRP. PlanAutomate solves this problem by seamlessly synchronizing projects, procurement, and production in a single system, keeping ICM’s entire operation aligned and running efficiently.
Virtually overnight, our project managers had information at their fingertips. They knew what the status of their projects were immediately.
Tim Allen – CFO at ICM
Z Modular Builds Steel-Strong Communities with PlanAutomate
Z Modular is transforming modular construction with precision-engineered, steel-framed developments. By reinventing traditional building and construction processes, they are driving efficiency, consistency, and scalability—and they chose PlanAutomate to help make it happen.
With a vision to seamlessly integrate ETO manufacturing and construction, Z Modular needed a solution that could unify design, engineering, procurement, manufacturing, shop floor control, and final installation into a single, cohesive system. PlanAutomate provided the comprehensive project platform to bring this vision to life, enabling Z Modular to streamline operations and redefine the future of modular construction.
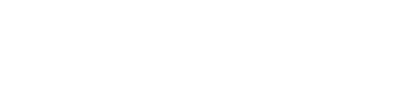
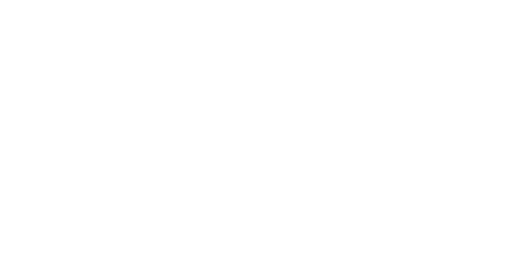
DPR Construction Transforms Pod Building with PlanAutomate
SurePods, a DPR Construction company, specializes in delivering custom, ready-to-install bathroom pods for healthcare, hospitality, and multi-living projects. Their highly complex, project-driven business requires seamless coordination across design, engineering, procurement, manufacturing, shop floor control, delivery, and installation.
Like many project-based businesses, SurePods previously relied on disconnected applications and spreadsheets for project management, leading to inefficiencies and lack of visibility. They needed a comprehensive solution to unify processes, link projects with production, develop a project-driven MRP, and manage costs from estimation through execution.
PlanAutomate provided the end-to-end system SurePods needed—bringing every aspect of their operations together into a single, integrated platform to optimize efficiency, accuracy, and control.
Anaergia Powers a Sustainable Future with PlanAutomate
Anaergia is a global leader in waste-to-energy innovation, transforming solid waste, wastewater, and agricultural byproducts into renewable energy. Their business spans engineering, design, and construction of advanced waste conversion plants, all with the goal of building a more sustainable future.
At Anaergia, every initiative is a project, and PlanAutomate is at the core of managing them. PlanAutomate delivers full financial visibility and control, ensuring projects stay on track and profitable. It also optimizes planning and operations throughout the entire project lifecycle, enabling Anaergia to efficiently execute its mission of turning waste into valuable resources.
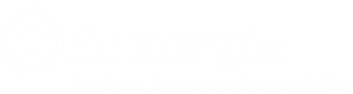
More customers we have helped transform with Project Automation
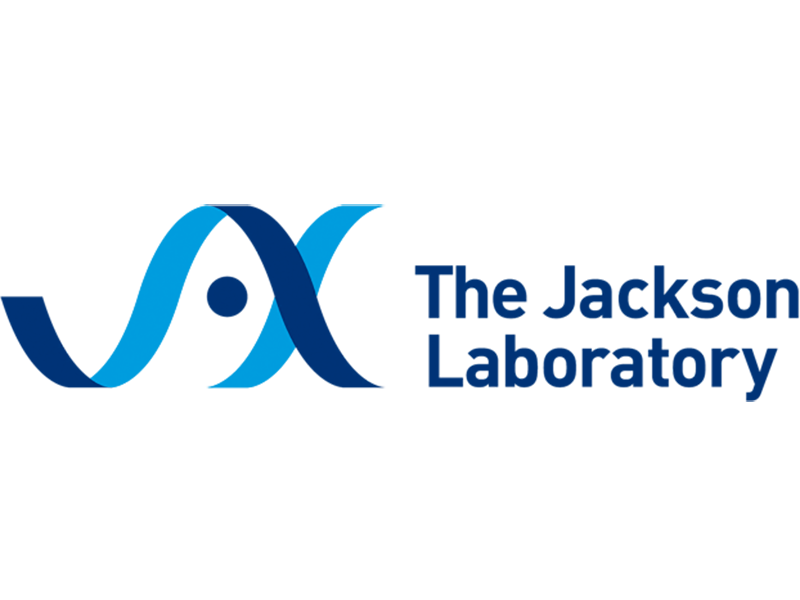
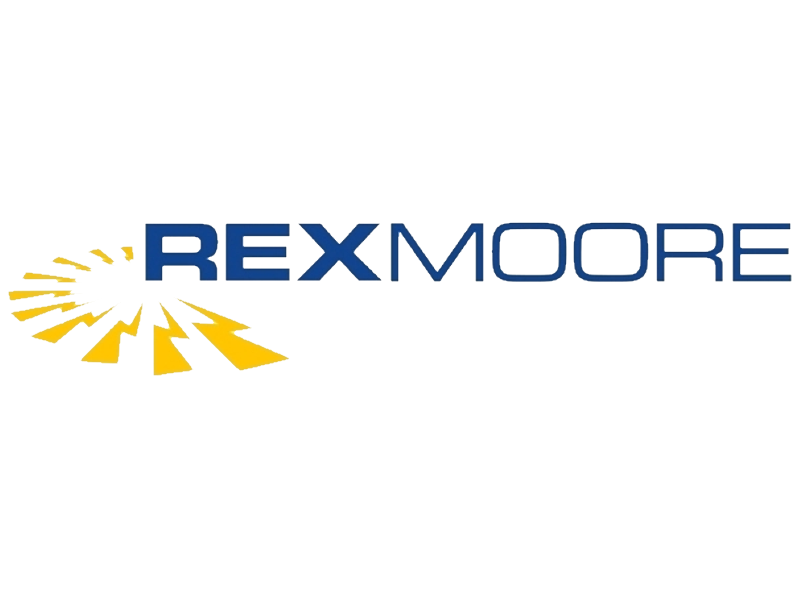
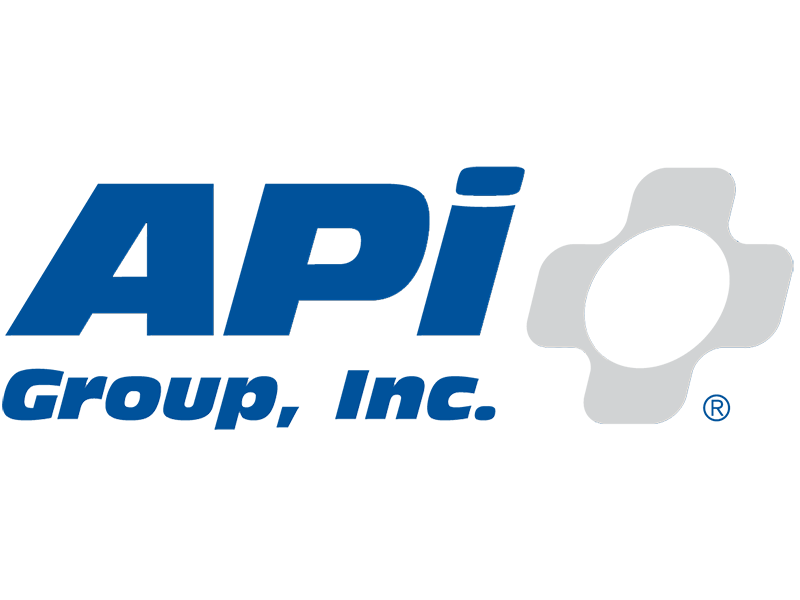
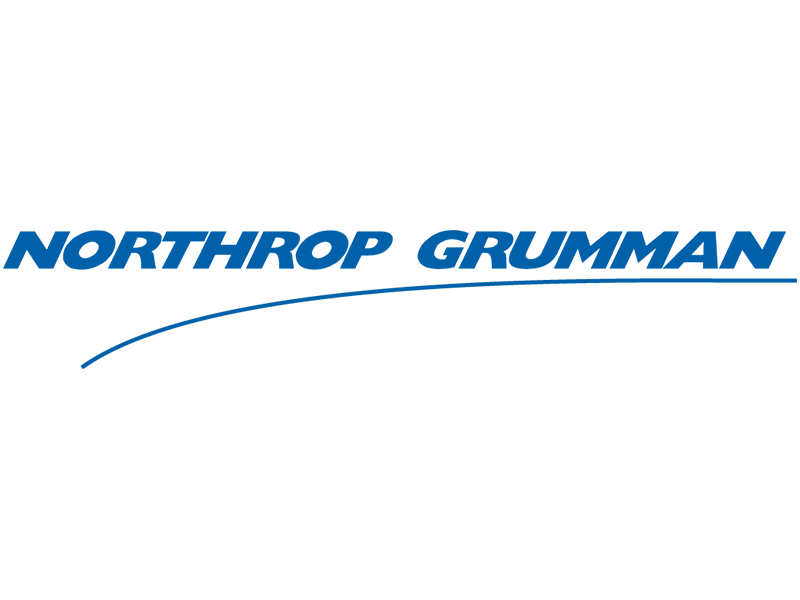
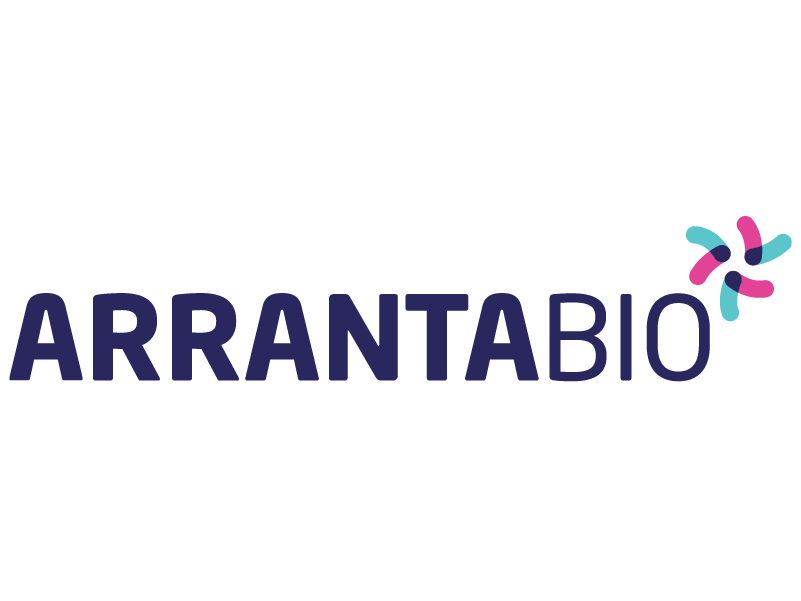
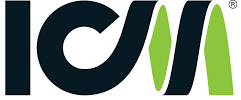
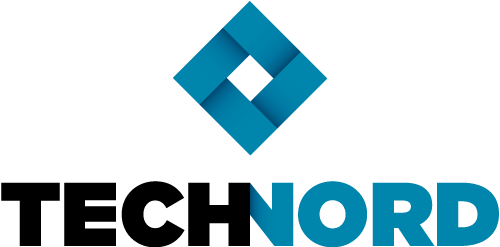
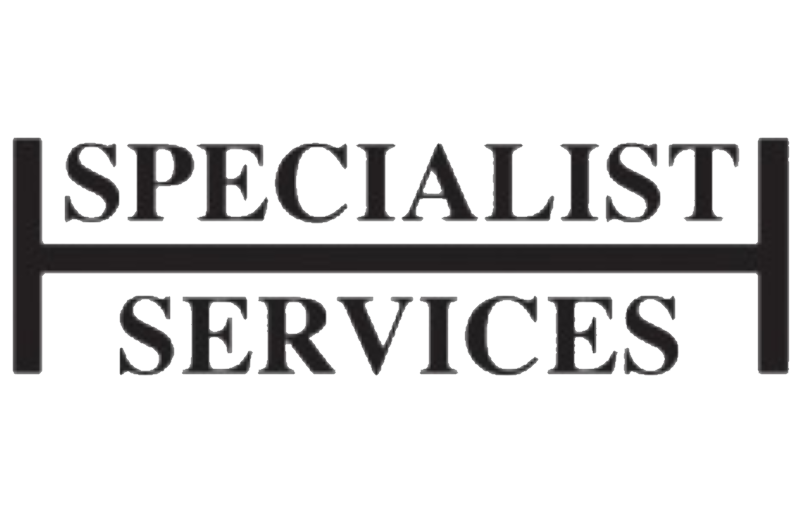
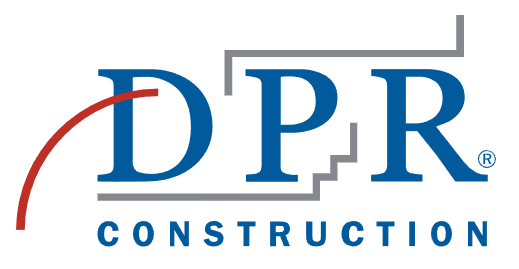
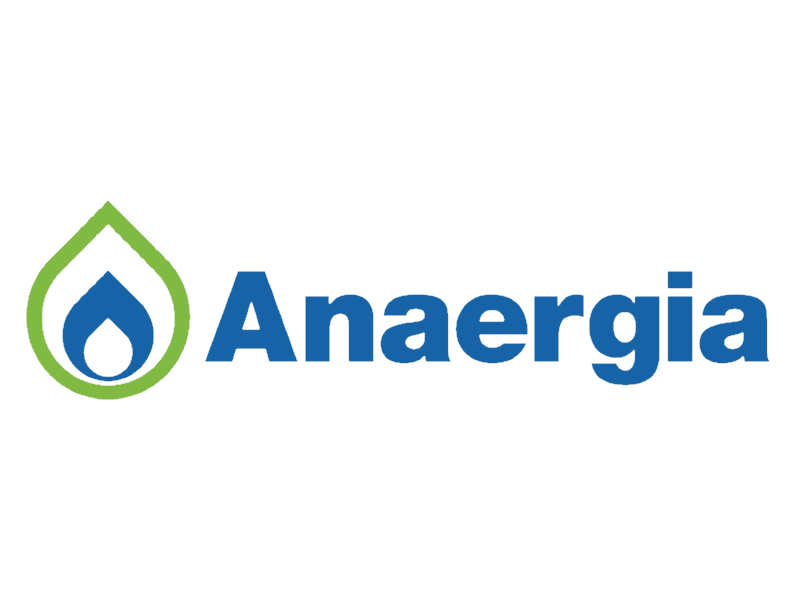
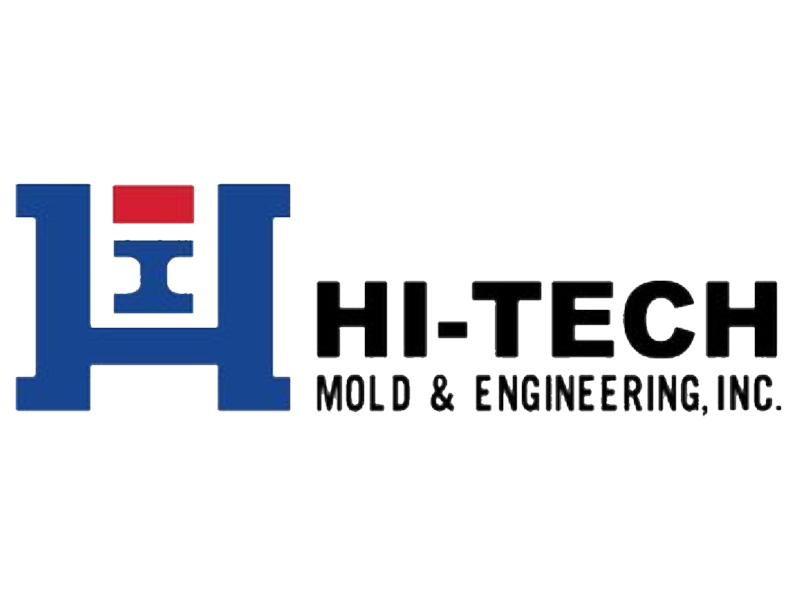
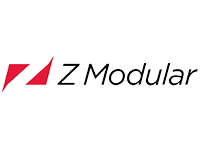
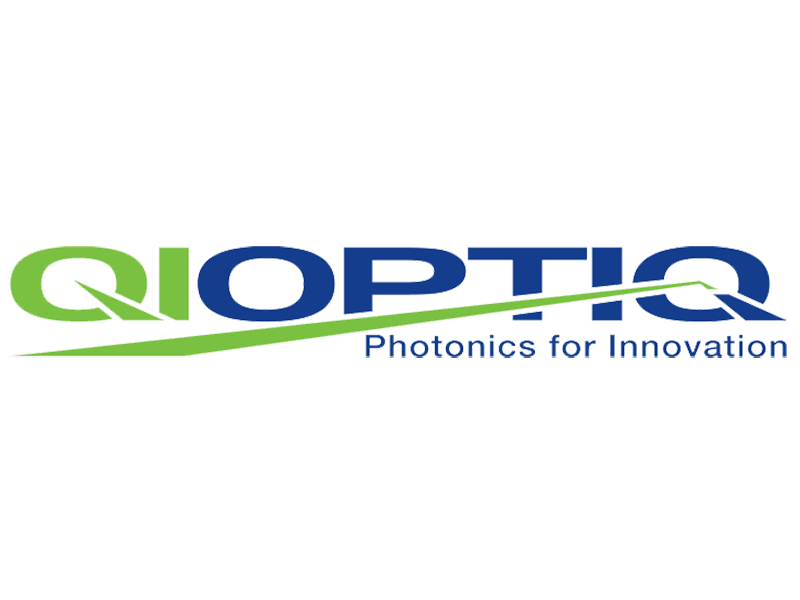
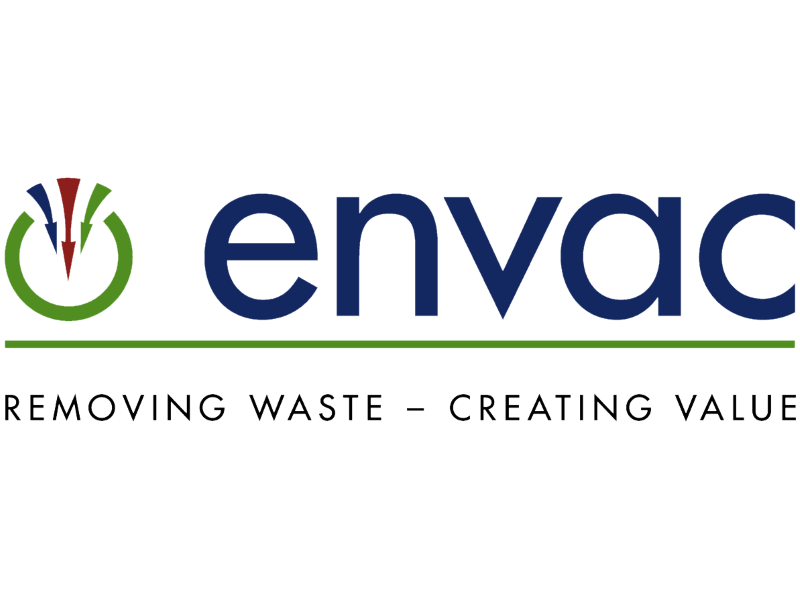
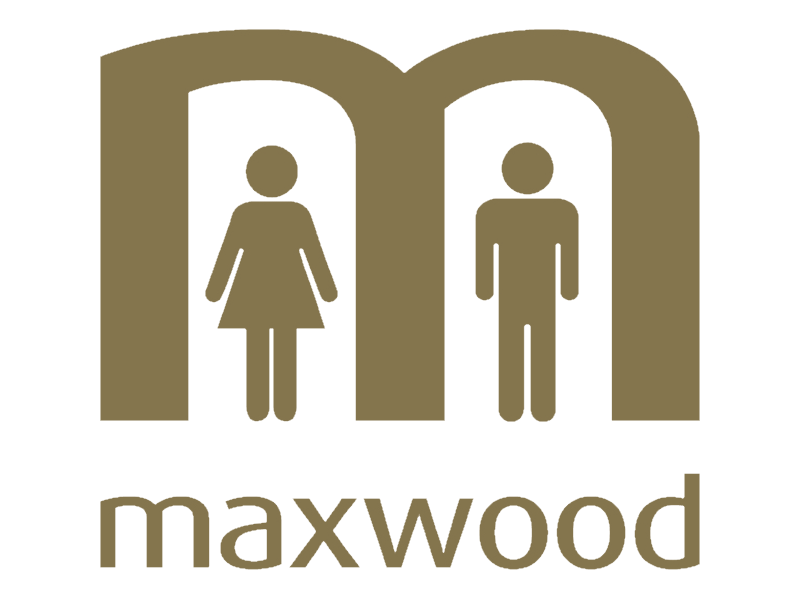
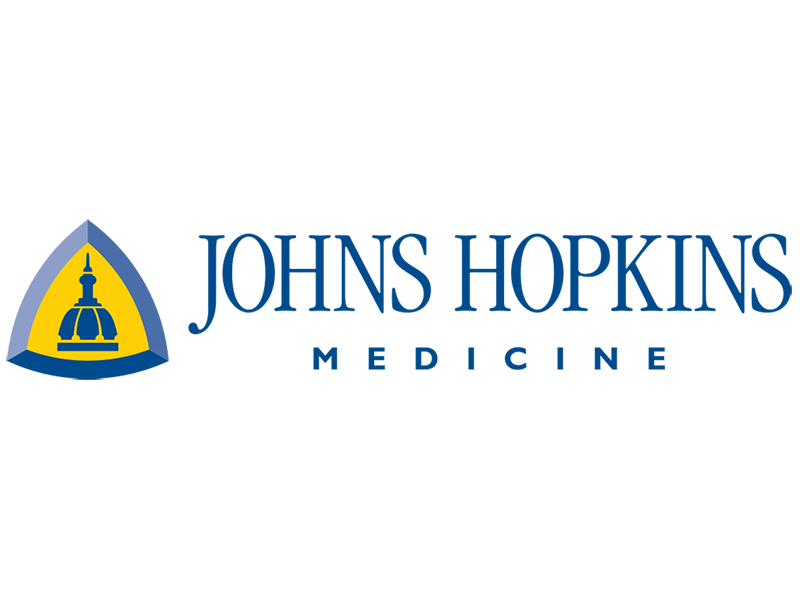
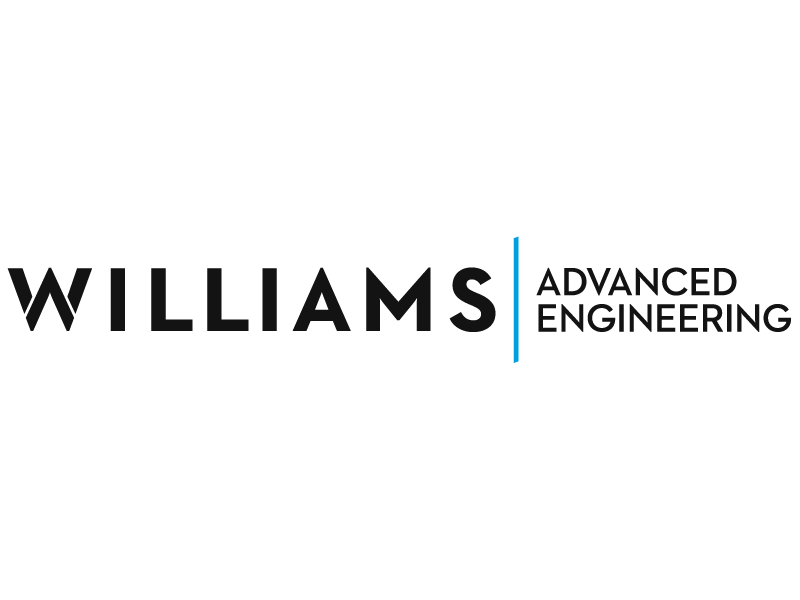
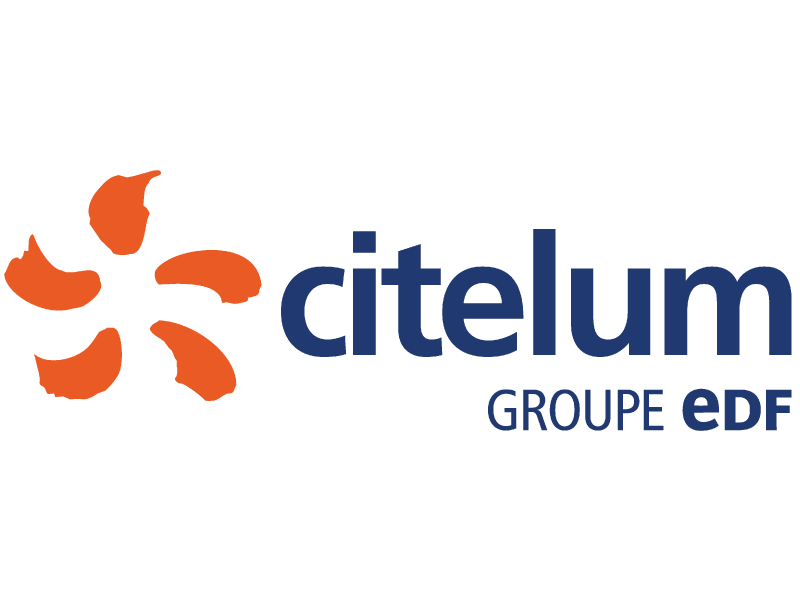
Is PlanAutomate a Good Fit for You?
Schedule a consultation
Find out if your company is a candidate for Project Automation. We will discuss your business, your current challenges, and show you where PlanAutomate may be able add value to your business.
It is easy and only takes a short amount of time.
Discover if PlanAutomate’s Project Automation is right for your company.
Schedule a consultation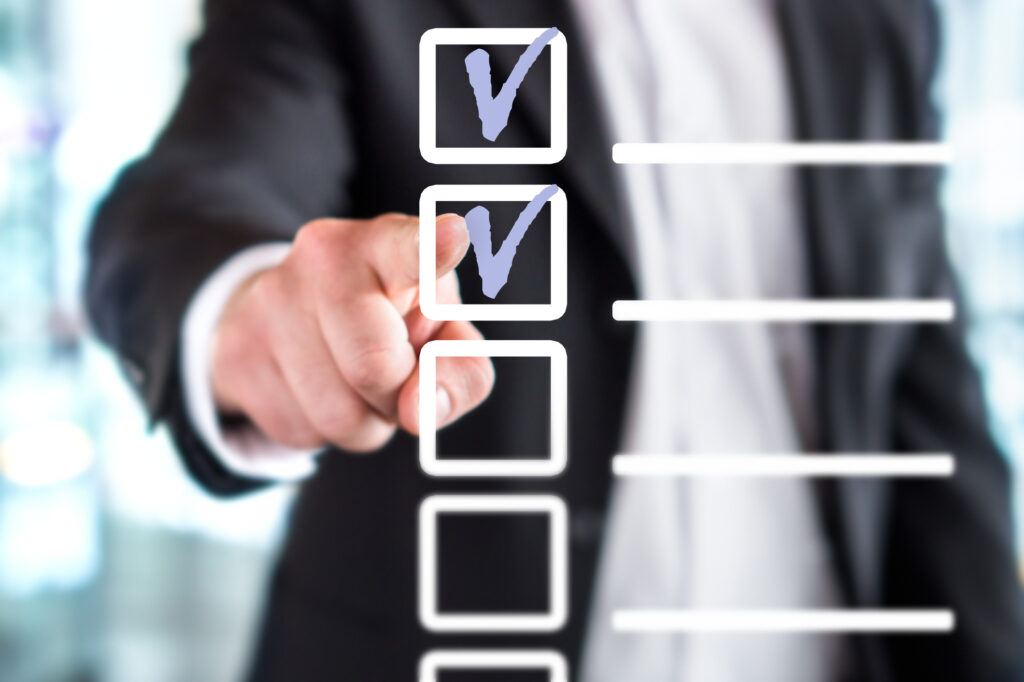
Ready to talk about project automation?
Reach out to us today to schedule a consultation.
Get Started